
A SPECIALIZEDMANUFACTURER
For decades, Dextrite has specialized in the design and production of fluorescent crushers. Having developed cutting-edge expertise in the disposal of used bulbs meeting environmental and safety standards, Dextrite holds CSA certification and has the innovative control tools for the safe destruction of fluorescent bulbs.
Basic features
Dextrite’s unique and innovative features allow it to stand out in the industry with a distinctive product for the safe destruction of fluorescent bulbs.
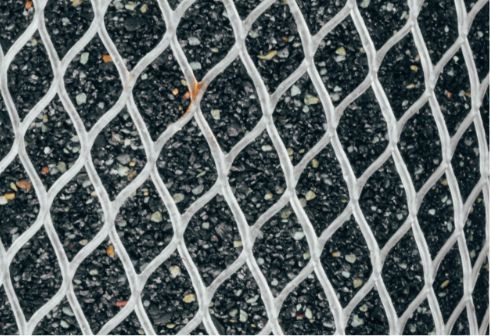
Activated-carbon
filtration system
Dextrite crushers are fitted with an activated carbon filtration system designed to recover mercury and phosphorous vapors.
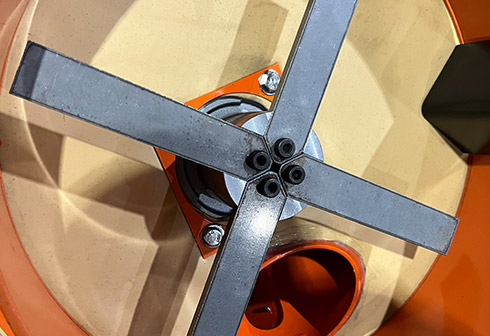
4 solid
blades
Crushing systems have 4 metal blades producing finer glass particles for more bulbs per drum.

Sleeve
system
The patented PolySleeve system allows drums to be changed safely, without subjecting the handler to direct exposure.
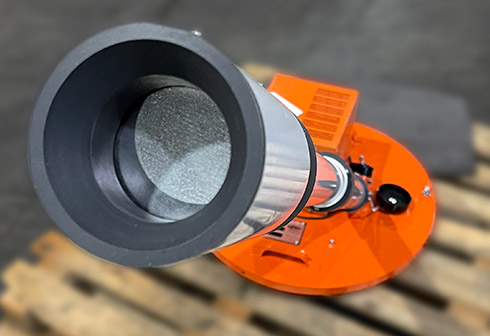
Automatic
shut-off valve
To avoid exposing the handler to vapors or broken glass, bulb-insertion chutes are fitted with an automatic shut-off valve.
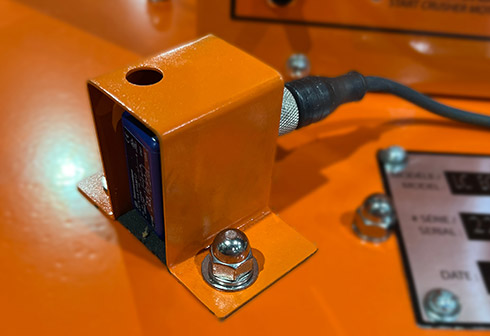
Optical
sensors
Used to count the number of crushed bulbs per drum as well as evaluate filter saturation, these sensors serve to avoid exposure to mercury and phosphorous vapors and dust.
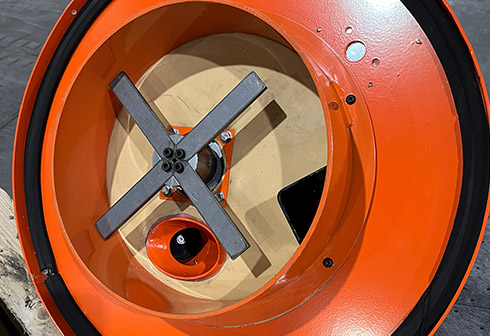
Double-walled
crushing chamber
Even during the crushing process, the double wall makes it possible to limit noise to no more than 65 decibels.
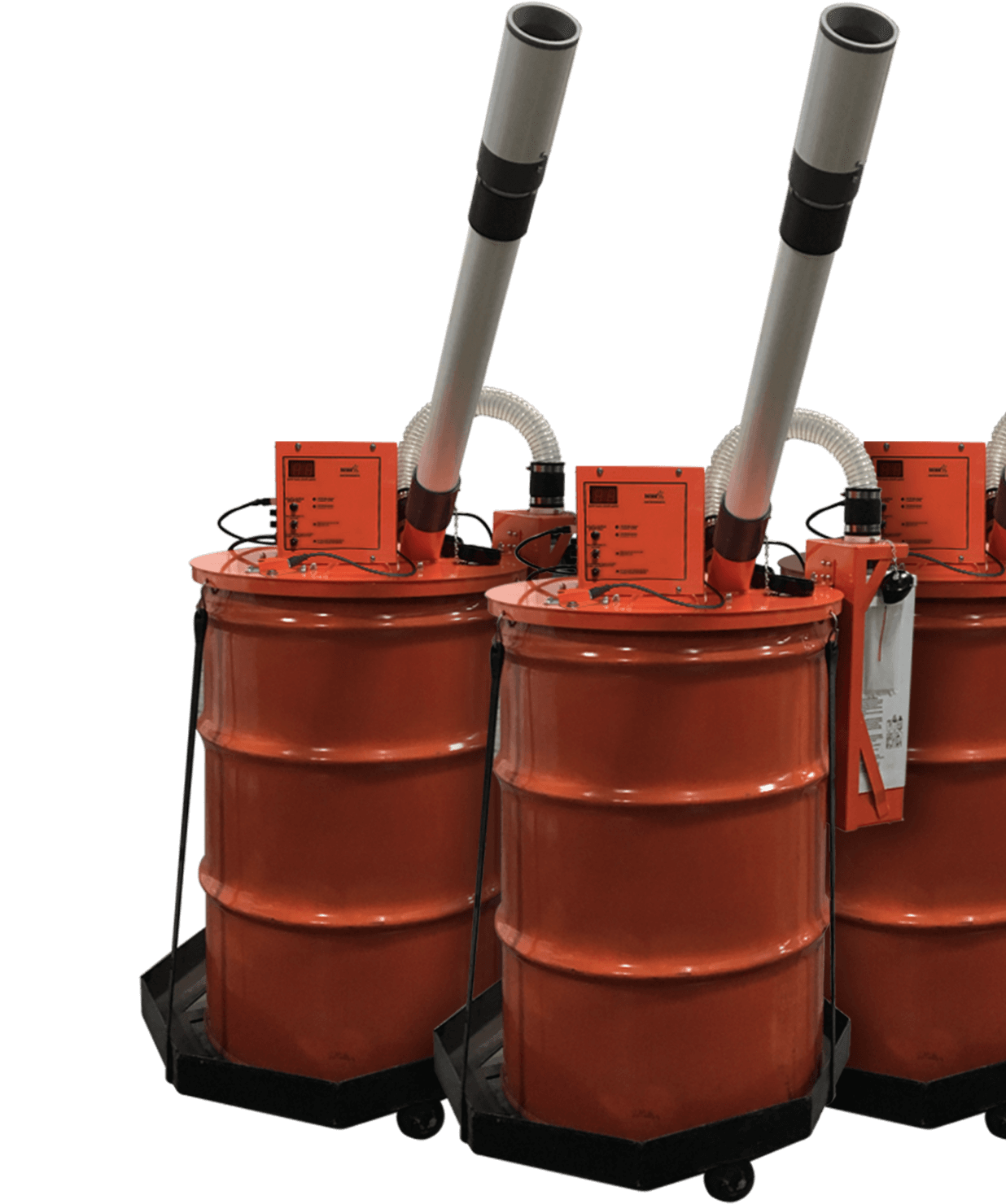
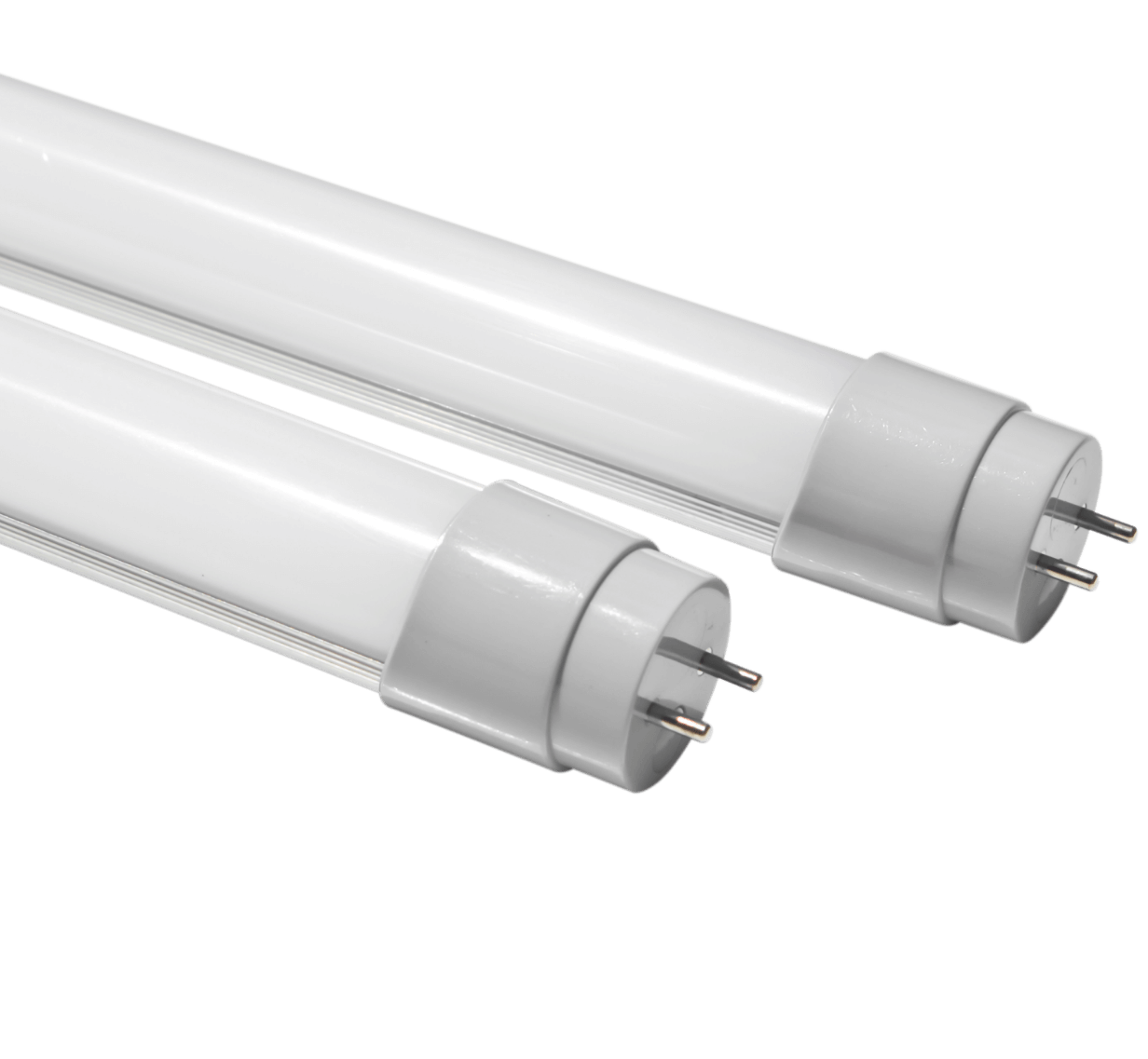
Costs and safety
Hazardous materials
Related dangers
Significant advantages
Reduced volume
of recyclable materials
Opting to crush fluorescent bulbs close to their replacement site considerably reduces the volume of materials sent for recycling.
Cost savings
(recycling)
The Dextrite crusher makes it possible to reduce shipping costs, since the waste from crushed fluorescent bulbs is fully contained in an airtight drum.
Reduced
risks
Dextrite fluorescent bulb crushers reduce the release of mercury in the atmosphere to levels below the maximum acceptable concentration standard.